In order to fully understand the importance of the regular application for wire rope lubrication during the working life of stranded or full locked coil hoisting ropes, it is first necessary to analyze the function of any such lubricant.
a) Each wire in any wire rope construction must remain as free as possible from adjacent wires so it can move to accommodate its allocated share of the varying rope tension it has to endure. This is especially important when the rope is performing at high speed and/or under the high wire contact stresses encountered during hoisting. Rope design is intended to minimize inter wire frictional contact but only by good lubricating practices can this effect be fully accomplished.
b) The majority of hoist ropes utilized in shafts are subject to corrosion from one cause or another. Shaft water containing a high salt content, chemical fumes, and upcast shafts producing condensation, are among the more notable causes. Regardless of the cause, it is essential to guard against or retard the certainty of corrosive attack on the steel. Experience has shown that the application of galvanized wire is only partially successful because the finish soon wears off. Therefore, it is clear that in-service lubricants must possess the following qualities:
a) Penetrate easily into the rope.
b) Displace moisture from the internal and external surfaces.
c) Provide good corrosion protection both internally and externally.
d) Be resistant to emulsification.
e) Possess good rope adhesive properties.
f) Resist removal by mechanical forces.
g) Possess good anti-wear properties.
h) Be compatible with the lubricant already employed during rope manufacture.
It should be pointed out that in the case of full locked coil and many plastic enhanced hoisting ropes, in-service lubricant is confined solely to the outside wire. This is because the inner rope is already sealed off with adequate lubrication.
Without lubrication during the working life, wire ropes may suffer from premature withdrawal from service:
1) Premature wire breaks occurring in the ropes and caused by internal and/or external corrosion.
2) Premature wire breaks occurring at the strand interstices due to lack of proper inter strand movement.
3) Strand displacement, loose wires, and rope waving, leading to loss of cross section stability. Additionally, the correct lubricant is of key importance during rope manufacture. Through a German study (see chart below), it is proven that the proper lay-up lubricant can have a great effect on rope life.
The chart depicts:
• Wire rope un-lubricated
• Wire rope lubricated, but with general lubricant not designed for wire ropes
• Standard lubricant designed for wire rope wires
• Wire rope application-specific lubricant Plastic enhanced
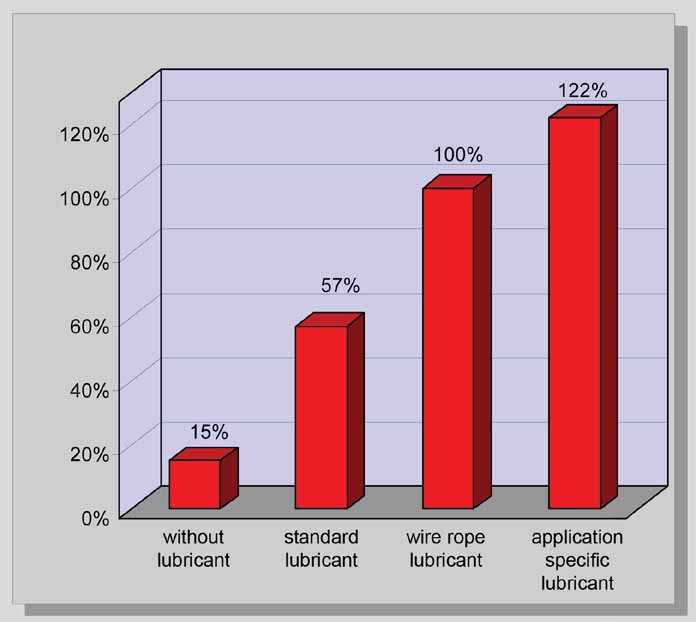
Northern Strands is an official supplier of Kirpatrick Lubricants in Canada.
Northern Strands is proudly Saskatoon, Saskatchewan owned and operated.